Investigation and Root cause analysis
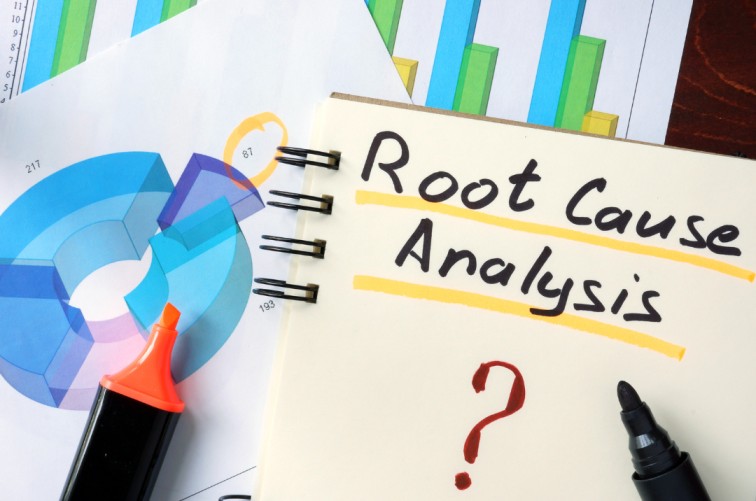
Achieving effective root cause analysis involves following a structured approach towards investigation and utilizing various techniques. Effective investigation and root cause analysis are critical processes for identifying the underlying causes of incidents, problems, or failures. By conducting a thorough investigation and determining the root cause, organizations can implement targeted solutions to prevent reoccurrence and improve overall performance. Based on our experience, lets discuss some steps you can take to conduct an effective root cause analysis:
- Establish clear objectives: Clearly define the purpose and scope of the investigation. Identify the specific incident or problem that needs to be addressed and set measurable goals for the analysis process.
- Define the problem: Clearly articulate the problem or issue you are investigating. Make sure the problem is specific and measurable, so that you can identify the root cause accurately.
- Align and assemble a competent team: Form a multidisciplinary/ Cross functional team with individuals who have relevant expertise and knowledge. Include representatives from different departments or areas involved in or impacted by the non-conformance. This diversity of perspectives will contribute to a more comprehensive analysis and thorough investigation.
- Gather information and data: Collect all relevant data and information related to the NC. This may include incident reports, historical data, interviews with people involved, witness statements, process documentation, records, and any other available evidence. Ensure the information is accurate, complete, and reliable.
- Identify relevant Causes: Analyse the collected information to identify the immediate causes and contributing factors that led to the incident. Look for both system and human factors, such as equipment failures, procedural deficiencies, training gaps, communication breakdowns, or human errors. This step involves asking probing questions and conducting interviews as necessary.
- Analysis techniques: Apply various analysis techniques, such as the 5 Whys, fishbone diagrams, fault tree analysis, or causal factor charting, to help identify the root cause(s) of the incident. These methods help uncover deeper underlying causes by systematically exploring cause-and-effect relationships. Utilize tools such as a cause-and-effect diagram to map out potential causes under various categories like people, process, equipment, materials, and environment. These tools will help you to uncover underlying causes rather than just surface-level symptoms that may contribute to the problem.
- Validate findings: Examine the data you have gathered and look for patterns or correlations. Identify any potential causal relationships between factors and the problem at hand. Prioritize the potential causes based on their likelihood and impact. Focus on the causes that have the highest potential for addressing the root issue effectively. Validate the identified root cause(s) with the team and relevant stakeholders. This step may involve additional data collection or consultation with subject matter experts.
- CAPA: Based on the identified root cause(s), develop effective corrective actions and recommendations to prevent future occurrences. The actions should be SMART (specific, measurable, achievable, relevant, and time-bound). Prioritize the actions based on their potential impact and feasibility of implementation.
- Implement, Review and Effectiveness check: Execute the corrective actions and monitor their implementation. Assign responsibility for each action item, set deadlines, and track progress. Regularly review and update the status of the actions to ensure accountability and timely completion. After implementing the corrective actions, periodically review the effectiveness of the measures and their impact on preventing incidents. Monitor relevant metrics and indicators to assess the progress made.
Please note that effective investigation and root cause analysis require a commitment to transparency, open communication, and a learning culture within the organization. It's essential to address the underlying causes rather than just treating the symptoms for a short term clearance.
Process workflow
Note: Process begins from Non-conformance workflow after quality contact (QC) has defined objective for NC and determined that an investigation is required.